Comprehensive Guide to Membrane Rubber: Advantages, Types, and Applications
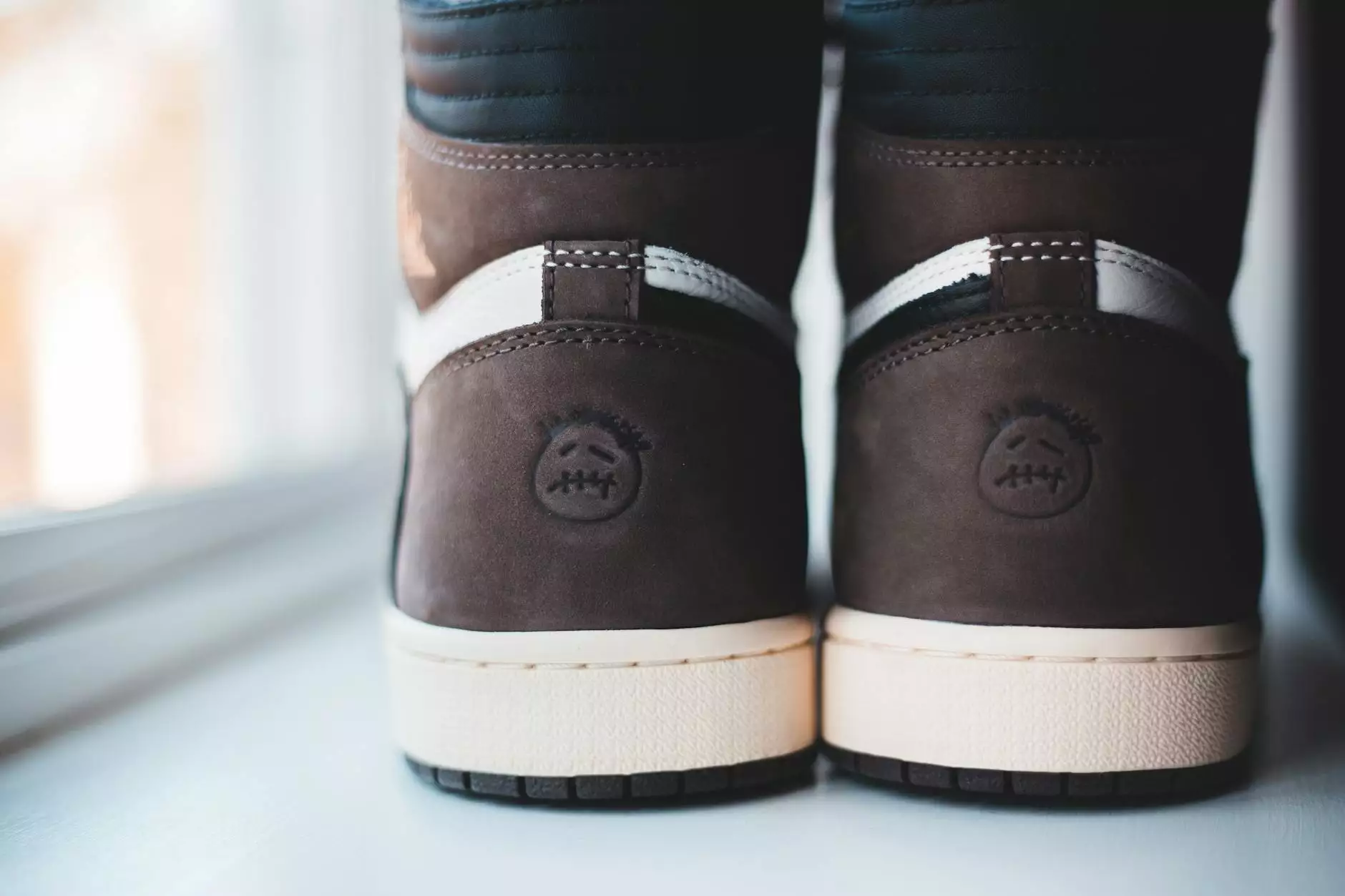
In the realm of industrial manufacturing and engineering, membrane rubber stands out as a pivotal material underpinning a multitude of applications. Its versatility, durability, and adaptability make it an indispensable element in sectors such as vacuum technology, chemical processing, water treatment, and sealing solutions. As industry demands grow increasingly sophisticated, understanding the nuances of different types of membrane rubber, their specific applications, and how they can enhance operational efficiency is critical for engineers, procurement specialists, and business owners alike.
What is Membrane Rubber? An In-Depth Overview
Membrane rubber refers to a specialized type of elastic material designed to act as a flexible barrier or diaphragm, capable of enduring significant mechanical stress while maintaining elastic integrity. These membranes are crafted from various rubber compounds and synthetic materials that confer unique properties suitable for different environments and requirements. They are primarily utilized to create airtight or fluid-tight seals, protect sensitive equipment from external elements, or facilitate controlled flexing in machinery.
The Crucial Role of Membrane Rubber in Modern Industry
From vacuum presses to industrial filtration systems, membrane rubber is central to many technological innovations. Its ability to form durable, flexible barriers ensures the optimal performance of devices and systems by providing:
- Leak-tight seals that prevent contamination or loss of fluids
- Elasticity to accommodate movement and thermal expansion
- Chemical resistance to withstand aggressive substances
- Weather and UV resistance for outdoor applications
- Longevity reducing maintenance and replacement costs
Types of Membrane Rubber and Their Unique Features
Choosing the appropriate type of membrane rubber depends on the specific application, environmental conditions, and desired lifespan. We explore the most common variants below:
Silicone Membrane
Silicone membranes are renowned for their exceptional flexibility, temperature resilience, and weather resistance. Withstanding temperatures ranging from -60°C to +230°C, silicone membranes are ideal for high-temperature environments and applications requiring excellent chemical inertness. They are frequently used in food processing, medical devices, and electronics because of their non-reactive nature.
Rubber Membranes
Traditional rubber membranes, often made from natural or synthetic rubber (such as Buna-N, EPDM, or SBR), excel in applications requiring elasticity and toughness. They provide reliable sealing solutions in hydraulic systems, water treatment, and industrial machinery. The key advantages include ease of installation, cost-effectiveness, and resistance to wear and tear.
Natural Rubber Membranes
Derived from latex sap, natural rubber membranes offer outstanding tensile strength, elasticity, and resilience against fatigue. They are highly suitable for vacuum systems, where a tight seal is essential, and the environment involves moderate chemical exposure. Their natural properties make them a preferred choice in applications demanding high flexibility and low permeability.
Specialty Membranes and Composite Options
Advances in material science have led to composite membranes that combine multiple rubber compounds with synthetic materials, providing tailored solutions. These are often used in demanding environments such as chemical processing plants or offshore platforms, where stability under extreme conditions is vital.
Applications of Membrane Rubber in Industry
The diverse properties of membrane rubber enable it to serve a broad spectrum of industrial applications, including but not limited to:
Vacuum System Parts
Within vacuum technology, membrane rubber forms the core sealing components in vacuum presses and systems. It ensures airtight conditions essential for processes such as lamination, composite material manufacture, and vacuum forming. Its flexibility enables it to accommodate the movement and pressure fluctuations typical in vacuum operations, thereby maintaining system integrity over extended periods.
Buy Membranes for Manufacturing Equipment
Industrial businesses often require high-quality membranes for machinery maintenance, upgrades, and new installations. Purchasing durable, certified membranes ensures efficient operation, reduces downtime, and minimizes replacement costs. Leading suppliers offer a wide selection of membranes tailored for specific applications, whether for chemical resistance, temperature tolerance, or mechanical strength.
Silicone Membranes in Medical and Food Industries
Because of their biocompatibility and resistance to temperature and chemicals, silicone membranes find extensive use in medical devices, sterilization equipment, and food processing machinery. Their inert nature prevents contamination, making them ideal for sensitive applications where hygiene and safety are paramount.
Rubber Membranes in Water Treatment
In water treatment facilities, rubber membranes are critical components in reverse osmosis systems, filtration units, and chemical dosing equipment. They provide a leakproof barrier that maintains system performance and ensures safety and environmental compliance.
Choosing the Right Membrane Rubber: Factors to Consider
Selecting the perfect membrane rubber involves evaluating several key parameters:
- Chemical Compatibility: Ensuring resistance to the fluids or gases involved.
- Temperature Range: Matching the membrane’s thermal tolerance to operational conditions.
- Mechanical Strength: Assessing tensile strength, tear resistance, and flexibility requirements.
- Environmental Conditions: Considering exposure to UV rays, ozone, weather, or aggressive chemicals.
- Thickness and Size: Adapted to specific system dimensions and sealing needs.
Why Quality Membrane Rubber Matters for Your Business
Investing in high-grade membrane rubber is pivotal for ensuring the reliability and longevity of equipment. Superior membranes reduce maintenance frequency, prevent costly leaks or failures, and enhance overall productivity. Working with trusted suppliers like vacuum-presses.com guarantees access to certified materials that meet industry standards.
Innovation and Future Trends in Membrane Rubber Technology
The field of membrane rubber is constantly evolving with new materials and manufacturing techniques aimed at addressing emerging challenges:
- Sustainable and eco-friendly membranes: Developing biodegradable and recyclable options to reduce environmental impact.
- Enhanced chemical resistance: Using advanced composites to withstand aggressive chemicals in harsh environments.
- Smart membranes: Incorporating sensors and IoT technology for real-time monitoring of membrane integrity.
- Nanotechnology integration: Improving strength, permeability, and durability at the molecular level.
Partnering for Success: How to Source High-Quality Membrane Rubber
Trustworthy suppliers, with expertise in manufacturing and distributing membrane rubber, are key to achieving optimal results. Look for vendors who offer:
- Certified and tested materials for compliance with industry standards
- Customized solutions tailored to specific operational needs
- Technical support and consultancy for selecting the right membrane type
- Prompt delivery and reliable supply chain
Conclusion: Unlocking the Potential of Membrane Rubber
In conclusion, membrane rubber is more than just a sealing material—it is a fundamental component that advances modern manufacturing, enhances system reliability, and promotes sustainable industrial practices. Whether you need silicone membranes for high-temperature applications, natural rubber membranes for vacuum systems, or custom composite solutions, choosing the right product from a reputable provider can significantly impact your business outcomes.
By understanding the diverse types and applications of membrane rubber, making informed purchasing decisions, and embracing ongoing technological innovations, your enterprise can operate more efficiently, with lower costs and higher safety standards. Explore the extensive selection available at vacuum-presses.com and ensure your operations are equipped with the best membrane solutions available today.