The Importance of **Custom Mold Makers** in Modern Metal Fabrication
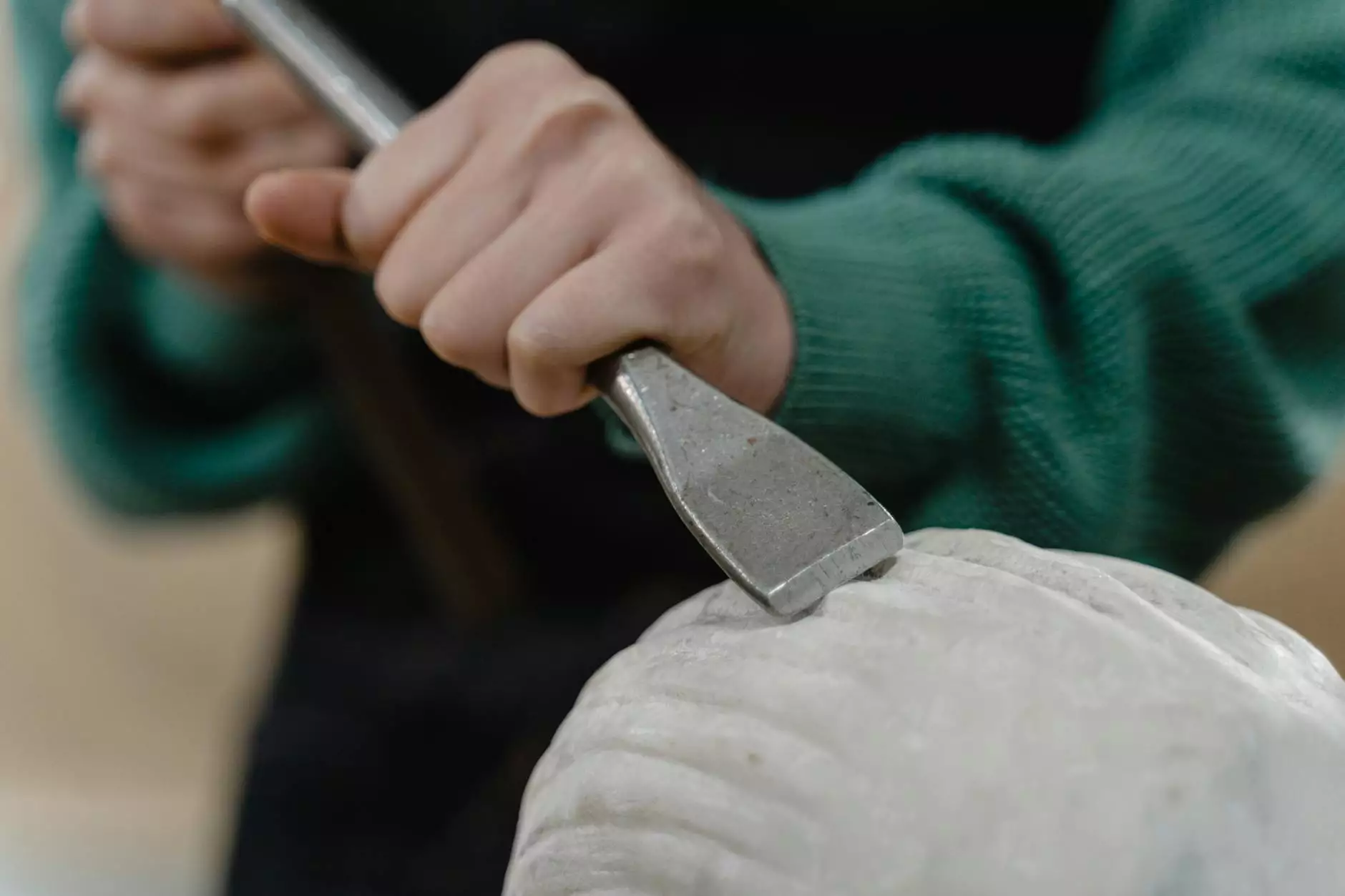
In the world of manufacturing, the role of custom mold makers cannot be overstated. As businesses look towards innovation and efficiency, the focus on high-quality molds becomes paramount. With the increasing demand for precision and customized solutions, understanding the value of these skilled artisans is essential for success in metal fabrication. In this comprehensive article, we delve deep into the realm of custom mold making, exploring its significance, advantages, and impact on the industry at large.
Understanding Custom Mold Making
Custom mold making is a specialized process that involves creating molds tailored to specific requirements of various industries, particularly in metal fabrication. These molds serve as the foundation for producing a wide range of products, from automotive parts to consumer goods. The process typically includes several stages:
- Design: Utilizing CAD (Computer-Aided Design) software to craft precise mold specifications.
- Material Selection: Choosing the right materials (like steel, aluminum, etc.) for durability and performance.
- Fabrication: The actual production of the mold using advanced machining techniques.
- Testing: Conducting trials to ensure the mold meets design specifications and functional requirements.
- Finishing: Applying surface treatments to enhance durability and reduce wear.
The Benefits of Hiring Expert Custom Mold Makers
Investing in custom mold makers provides numerous benefits to businesses looking to optimize their production processes:
1. Tailored Solutions for Unique Needs
Every business has unique product specifications. Custom mold makers understand this and provide tailored solutions that meet specific requirements, ensuring that the final product is exactly what the client envisioned.
2. Enhanced Quality Control
With expertise in design and manufacturing, seasoned mold makers can guarantee the highest quality standards. This leads to fewer errors and defects in the production process, ultimately saving companies time and money.
3. Increased Production Efficiency
Utilizing precision-crafted molds can significantly streamline production lines. Efficient molds reduce cycle times, allowing businesses to produce more units in a shorter timeframe, and respond swiftly to market demands.
4. Cost Effectiveness in the Long Run
While the initial investment in custom molds may seem significant, the long-term savings from reduced waste, decreased downtimes, and lower rework costs can dramatically enhance profitability.
Key Industries Benefiting from Custom Mold Makers
The implications of using custom mold makers spread across various sectors:
- Automotive: Precision molds are required for producing parts such as engine components, chassis parts, and interior fittings that meet safety and performance standards.
- Aerospace: Molds for aerospace components must meet rigorous industry regulations, making custom designs critical for ensuring safety and reliability.
- Consumer Electronics: Custom molds play a vital role in creating housings and parts that are both functional and aesthetically pleasing.
- Medical Devices: Given the critical nature of medical devices, custom molds must be expertly crafted to ensure compliance with stringent health regulations.
- Home Appliances: Custom mold making allows for the production of unique designs while maintaining functionality and efficiency.
Choosing the Right Custom Mold Makers
Selecting the right custom mold makers can be a daunting task. Here are some essential factors to consider:
1. Expertise and Experience
Look for mold makers with a proven track record in the industry. Their experience contributes to their understanding of complex requirements and potential challenges.
2. Advanced Technology
Ensure that the mold makers utilize the latest technology and equipment in their processes. State-of-the-art tools enhance precision and efficiency in mold creation.
3. Customer-Centric Approach
Effective communication is vital. Choose a company that listens to your needs and works collaboratively throughout the process.
4. Quality Assurance
Review their quality control measures to ensure they align with your company's standards. A commitment to quality is crucial for long-term partnerships.
5. Flexibility and Scalability
Your business needs can change over time. Opt for mold makers capable of adapting to your evolving requirements and capable of scaling production as necessary.
Innovations in Custom Mold Making
The field of custom mold making is continually evolving. Here are some recent innovations shaping the industry:
- 3D Printing: Incorporating 3D printing technology allows for rapid prototyping, reducing the time from conception to production.
- Smart Molds: Integrating sensors into molds provides real-time data on temperature and pressure, enabling better control during the manufacturing process.
- Eco-Friendly Materials: Many mold makers are now using sustainable materials and processes, reducing environmental impact and catering to eco-conscious businesses.
- Advanced CAD Software: Improved design software enables more complex and precise mold designs, pushing the limits of what’s possible in mold making.
Conclusion: The Future of Custom Mold Making
As industries continue to push for innovation and efficiency, the role of custom mold makers will remain critical. By providing tailored solutions that enhance quality, operational efficiency, and cutting-edge technology, these experts are paving the way for the future of metal fabrication. Businesses that recognize and leverage the advantages of working with skilled custom mold makers will be well-positioned to thrive in an increasingly competitive landscape.
At DeepMould.net, we pride ourselves on being at the forefront of the mold-making industry. Our commitment to excellence ensures that we deliver the best in custom mold making services, tailored to meet your unique needs. Connect with us today to explore how we can help elevate your metal fabrication projects to new heights.